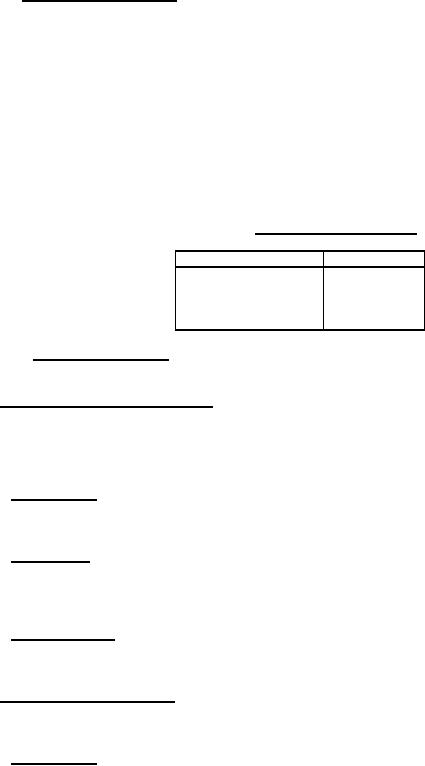
MIL-PRF-914C
4.6.3.2.4 Subgroup 3 (solderability). The subgroup 3 test shall be performed on an inspection lot basis for ER
parts. A sample shall be selected from each lot in accordance with table XV. As an option, the manufacturer may
use electrical rejects from the subgroup 1 tests for all or part of the sample. If there are one or more defects, the
inspection lot is rejected. The manufacturer may use one of the following options for corrective action:
a.
Each production lot that was used to form the failed inspection lot shall be individually submitted to the
solderability test. Production lots that pass are available for shipment. Production lots that fail can be
submitted to the rework procedures of 4.6.3.2.4b.
b.
The failed inspection or production lot is submitted to a 100 percent hot solder dip using an approved solder
dip process in accordance with 3.5.2.1 or other rework process. A subsequent solderability test shall then
be performed. If the lot passes, it is available for shipment; if the lot fails, the manufacturer may perform the
hot solder dip one additional time. If the lot fails to pass, the lot is considered rejected and shall not be
supplied to this specification.
TABLE XV. Solderability sampling plan.
Lot size
Sample size
1 to
3200
5
3201 to
10000
8
10001 to
35000
13
35001 and above
20
4.6.3.2.4.1 Disposition of samples. The solderability test is considered a destructive test and samples submitted to
the solderability test shall not be supplied on the contract.
4.6.4 PPM assessment (non-ER and ER). The manufacturer shall establish and maintain a system for assessing
the average outgoing quality in ppm of lots supplied to this specification. This ppm assessment should be based on
inspections performed on each inspection lot to verify that resistor networks meet dc resistance and tolerance
requirements. For ER resistor networks, this inspection shall occur after the group A, subgroup 1, 100 percent
screens have been completed.
4.6.4.1 Sampling plan. Minimum sample sizes for inspection lots shall be selected in accordance with table XIV.
For non-ER networks, the sampling system and plan used for the group A inspection (see 4.6.3.1) may be the basis
for assessing ppm.
4.6.4.2 Rejected lots. Any rejected lot shall be segregated from new lots and those lots that have passed the ppm
assessment. A rejected lot may be rescreened for the quality characteristic found defective in the sample and any
defects removed. A new second sample shall be randomly selected. If one or more defects are found, the lot is
rejected and shall not be supplied to this specification.
4.6.4.3 PPM calculations. PPM calculations shall be based on the accumulated results of the initial sample.
Calculations and exclusion shall be in accordance with EIA-554-1. (NOTE: PPM calculations shall not be based on
the second sample submission for a rejected lot as described in 4.6.4.2).
4.6.5 Group B inspection (ER only). Group B inspection shall consist of the tests specified in table XVI, in the
order shown. They shall be performed on sample units that have been subjected to and have passed group A
inspection.
4.6.5.1 Sampling plan. All qualified styles may be grouped together in a single sample. This can be accomplished
by proportion based on manufacturing percentages by style, equally divided by style, or by establishing an alternating
style sequence. In order to incorporate a style sampling grouping, a written description must be presented and
approved by the qualifying activity. This plan must assure that the grouping only combines styles of the same basic
design, encapsulation material, and the same element type.
20
For Parts Inquires call Parts Hangar, Inc (727) 493-0744
© Copyright 2015 Integrated Publishing, Inc.
A Service Disabled Veteran Owned Small Business